ISO/IEC 17025:2017 Analytical Services Laboratory (ASL) is accredited by the Standards Canada Council (SCC) through the Bureau de Normalisation du Québec (BNQ). For more info, For more info, click on these links: ISO/IEC 17025:2017 Certificate and the Scope of Accreditation
ISO 9001:2015 Pyrometallurgical characterization laboratory (PCL)
ISO 14001:2015 Environmental Management Systems (EMS)
State-of-the-art equipment
Well-prepared to carry out tasks from simple screenings to comprehensive pilot projects on a semi-industrial scale of a complete ore processing circuit
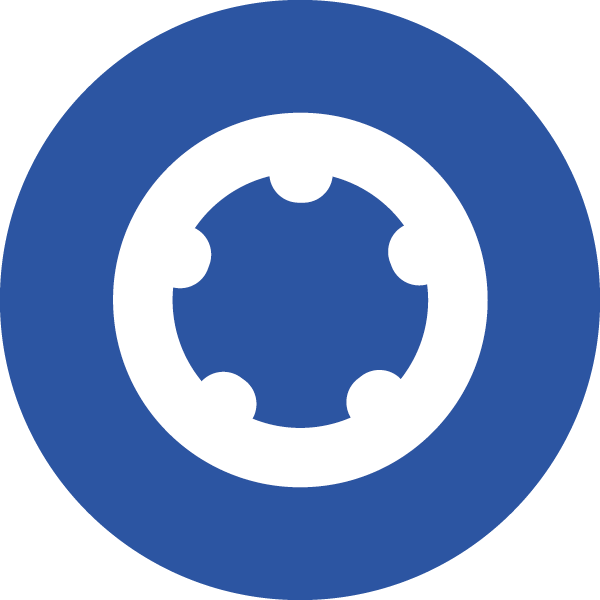
Comminution
Corem has a wide range of equipment to carry out pilot testing of comminution circuits. Most of it is modular and mobile; this allows flexible circuit configurations to meet clients objectives.
The comminution group has also developed expertise in the simulation of different types of mills and comminution circuits and owns recognized simulation software for grinding circuits (such as JKSimMet) in addition to in-house simulators.
Pilot plant equipment
HPGR (800 mm x 250 mm)
AG/SAG mills (6 ft x 2 ft)
Crushers
Jaw, cone and roll
Mills
Rod, ball and pebble
(12 in. x 12 in. to 30 in. x 60 in.)
Hydrocyclones
Sieves
Filters and thickeners
Available Tests
SAGDesign™ (Starkey)
Bond Work Indices:
Abrasion Work Index (Ai)
Ball Mill Work Index (WiB)
Rod Mill Work Index (WiR)
Isamill Signature Plot Test
Levin Work Index
Karra Work Index
Drop Weight Test (Axb)
Abrasion Test (ta)
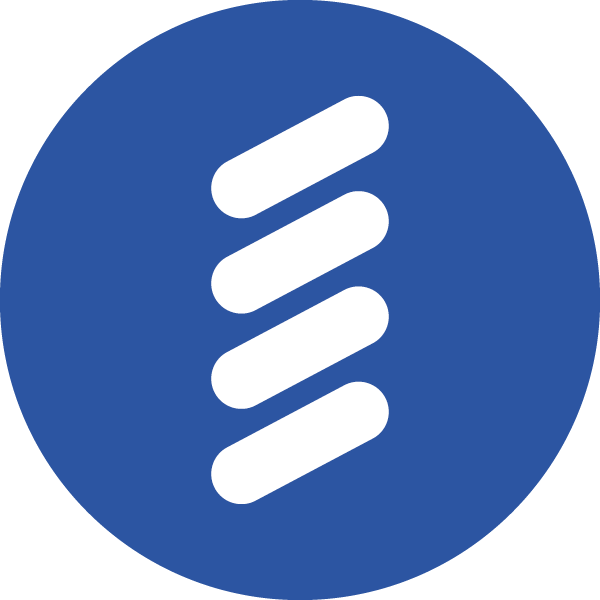
Physical separation
Corem has a wide range of gravimetric, magnetic and electrostatic separation equipment to conduct almost any task at the bench and pilot scales. In addition to standard equipment, such as spirals or hindered settlers, Corem possesses the last generation of gravity separators.
With those equipment and its expertise, Corem can push gravity separation up a notch and separate finer ore or minerals with low density differences or that are normally out of the range of traditional separation technologies.
Gravity separators
Spirales: Walkabout (lab scale), HC-33, H 9000W, HC 8000, WW6E, FM1, HG and MG Series, LD7, etc.
Enhanced gravity Separators: Falcon, Knelson and Mozley multi-gravity separators (MGS)
Hindered settlers: CFS 8 in. x 8 in. et 15 in. x 15 in., Floatex 18 in. x 18 in., Hydrosizer, Reflux Classifier (pilot scale)
Shaking tables: Wilfley tables (3, 4, 5 et 9 ft), Mozley table, air table
Others: Denver standard jig, Kelsey jig, All jig (pilot scale)
Magnetic separators
DRY
Low intensity / lab-scale
Sala Mortsell
High & medium intensity / Lab-scale
Carpco induced roll, Carpco lift mag, Frantz, Mini-Jones
High & medium intensity / Pilot scale
Carpco Hob mag
WET
Low intensity / Lab-scale
Sala laboratory
Low intensity / Pilot scale
Stearn (3 drums), Thune 500 and Thune 600
High & medium intensity / Lab-scale
Davis tube, wet high-intensity magnetic separator Carpco
High & medium intensity / Pilot scale:
SLon
Electrostatic separators
Carpco High tension separator
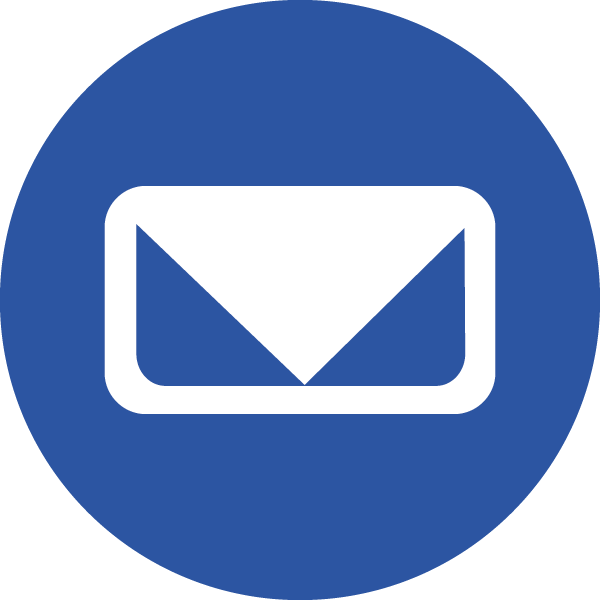
Flotation
Highly performing facilities and equipment enable COREM to manage the treatment of drill cores as well as bulk crushed rocks in samples from a few grams to hundreds of tonnes.
The pilot plant houses a wide range of equipment: mechanical cells, flotation columns and all the support equipment required to run a flotation circuit.
Development, validation or optimization of any flowsheet is possible at flowrates up to several hundreds of kilograms per hour.
Equipment
Denver flotation cells
(1,5 à 10 L)
Magotteaux flotation cells
(1,5, 2,5 et 5 L)
Semi-industrial flotation banks
(8 à 250 L)
Instrumented flotation columns
25 ft x 2, 4, 6 in. and 16 ft x 12 in.)
On stream analysis using LIBS technology
Portable flotation columns
Laboratories
The flotation laboratory is equipped with cells of various sizes, all equipped with monitoring instruments for an accurate control of each flotation test.
Metallurgical performances can be validated through lock cycle or semi-industrial continuous tests.
An applied mineralogy laboratory
An ISO / IEC 17025:2005 accredited chemical analysis laboratory
Corem is capable of addressing a very wide span of flotation issues, from developing flotation strategies based on ore-specific properties to explaining performance mishaps in existing plants.
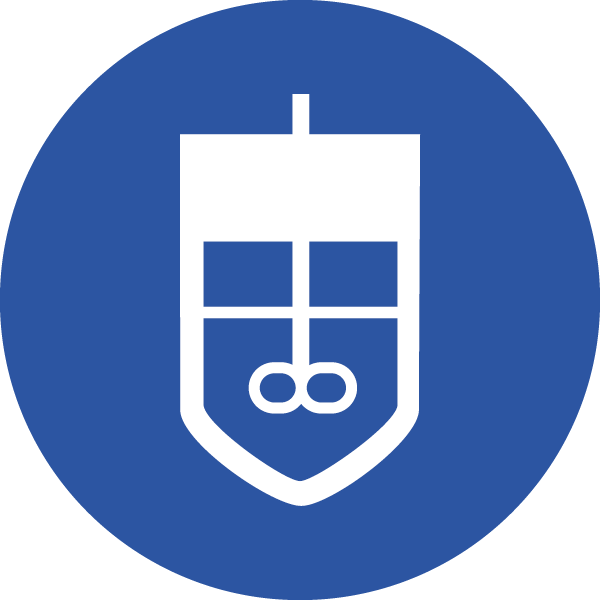
Extractive metallurgy
Corem maintains a complete hydrometallurgical sector for handling, at the laboratory and semi-industrial scales, all mineral acids and bases under high temperature or high pressure.
Whether in order to concentrate the metals of interest or to remove metal impurities in a non-metallic deposit such as graphite, the expertise of its team is well established and capable of providing substantial added value to every project Corem is entrusted with.
Equipment
2 to 2,000 L reactors
1 to 40 L autoclaves
Pressure filter and vacuum filter (horizontal and vertical)
Wet scrubber
Resin columns
Laboratories
From the results of mineralogical analyses carried out in COREM’s laboratories, a multidisciplinary team works together to develop all stages of a project and define an experimental flowsheet.
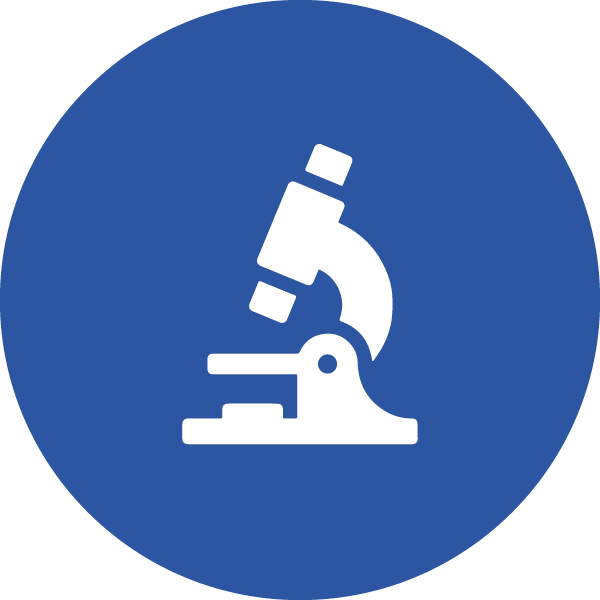
Mineralogy
Corem uses state-of-the-art equipment and follows standardised procedures to guarantee the preparation of representative samples out of bulk samples from the laboratory, the pilot plant or from the deposit.
Samples of any origin (crushing, grinding, sieving, shaking table separation, dense media separation, magnetic separation, etc.) can be studied in bulk or mounted into high quality polished or thin layer sections in COREM’s mineralogical laboratory.
Quantitative mineralogical studies
The MLA is used to conduct quantitative mineralogical studies on various ores and process samples.
Modal analysis
(mineral list and abundances)
Particle size distribution
Liberation of minerals of interest
(valuable and gangue minerals)
Elemental distribution
(valuable and contaminants)
Mineral associations
Theoretical recovery curves
Automated optical microscope
Corem has developed in-house an automated optical microscope for characterizing the microstructure of iron ore pellets
Applications |
Petrographic studies of new deposits |
Assessment of beneficiation potential of ore bodies |
Drill core characterization |
Study of process samples for troubleshooting |
Plant performance prediction |
Elemental and mineral deportment studies |
Iron ore pellets characterization |
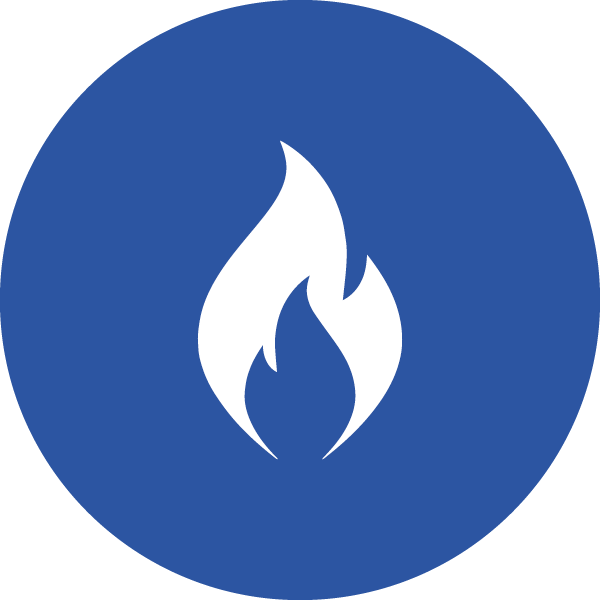
Pelletizing and thermal processes
Corem offers high and proven expertise in optimizing the chemical composition of various types of iron ore pellets and their firing cycle. Pot-grate or grate-kiln-cooler test rigs are used to optimize firing conditions for either the travelling grate or the grate-kiln processes. Pelletizing test work can be carried out at the:
Laboratory scale, using a balling tire or disk in combination with basket firing, with the capacity to fire up to six different samples in one test;
Pilot scale, using a 1 m pelletizing disk in combination with pot-grate or grate-kiln-cooler firing tests.
Corem can also determine pellet properties following their reduction at high temperature
Lumps, sinter and pellets
characterization
Physical tests | |
Cold Compressive Strength (CCS) | ISO 4700 |
Tumble indexes | ISO 3271 |
Blast furnace tests | |
Relative reducibility and R40 | ISO 7215, JIS 8713-1, ISO 4695 |
Swelling | ISO 4698 |
Static disintegration at low temperature | ISO 4696-1, 4692-2 |
Dynamic disintegration at low temperature | ISO 13930, HYL |
Reduction under load (RUL) | ISO 7992 |
Softening temperature | COREM |
Direct reduction tests | |
DR90 reducibility | ISO 11258 |
R180 reducibility | COREM |
Linder | ISO 11257 |
Clustering | ISO 11256, HYL |
HYL reducibility | HYL |
HYL swelling | HYL |
Lab and pilot scale equipment
Corem has all the equipment and necessary expertise to perform tests meeting the highest quality standards (ISO international standards, and other standards). Corem is an active member of the ISO/TC/102 committee for the development of ISO standards for iron ore and direct reduced iron ore. Corem chairs the CAC ISO/TC/102/SC3 Canadian sub-committee on physical testing. Corem’s pyrometallurgical characterization laboratory is certified ISO 9001:2015.
Extensive equipment for the characterization of binders, minerals, and pellets |
Balling tire (exploratory testing) |
0.5 m diameter pelletizing disk |
1 m diameter pelletizing disk (~ 500 kg/h iron ore) |
Roller deck screen |
Firing simulators for travelling grate and grate-kiln processes (pot-grate, pot-grate/rotary-kiln) |
Pot-grate basket firing |
Eirich mixer (micropelletizing) |
Komarek press (briquetting) |
Continuous rotary kiln (0.4 m diameter by 4.8 m length) |